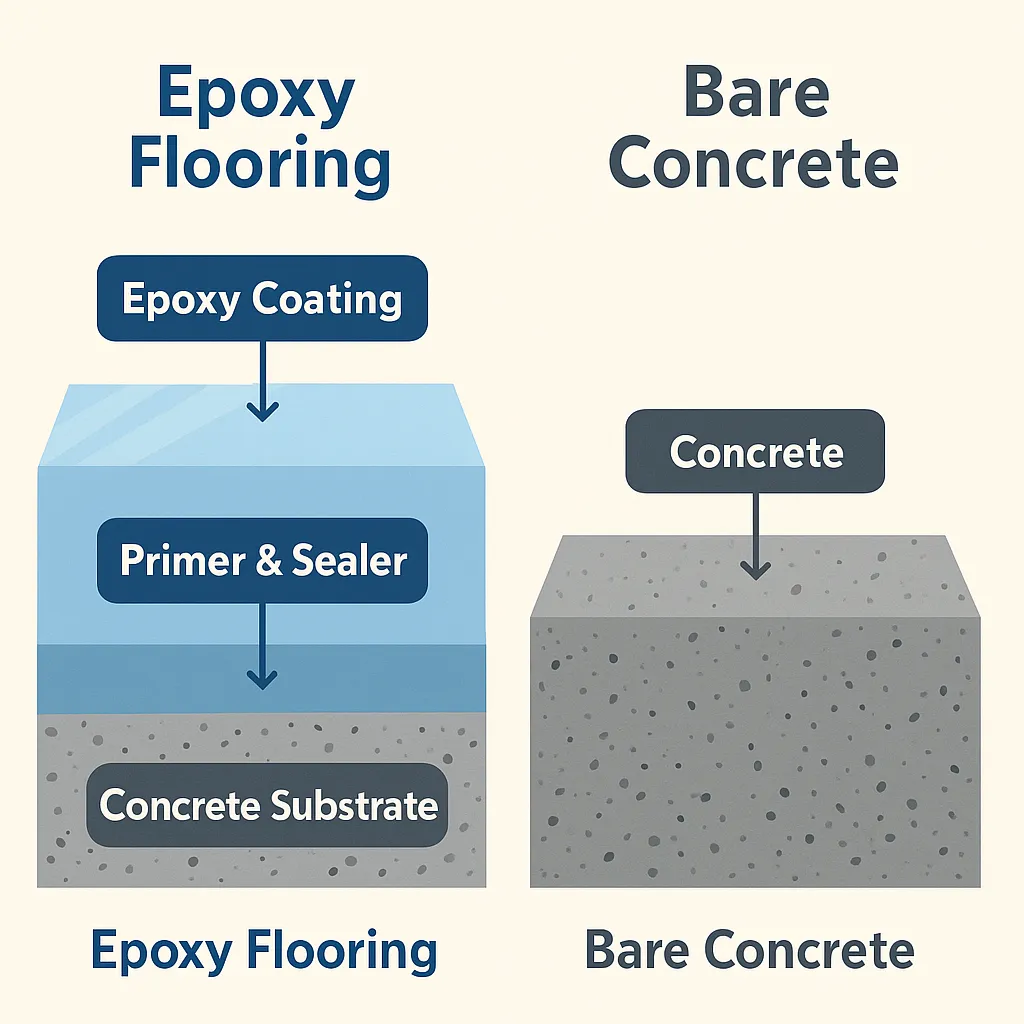
How to Choose a Pro Epoxy Installer (and Not Regret It)
How to Choose a Professional Epoxy Installer
Every time you pull into the garage, you see it. The spiderweb cracks. The dull, stained slab that refuses to look clean no matter how many times you sweep. You’re not alone—more than 60% of homeowners report dissatisfaction with their garage floors within the first five years of moving in.
The truth is, concrete takes a beating in the Midwest. Between brutal winters, hot tires, and the occasional oil spill, even the toughest slabs start to break down. That’s where epoxy comes in. Done right, it transforms tired concrete into a seamless, polished surface that holds up year after year.
But here’s the catch—not all epoxy installations are created equal. Choose the wrong installer, and you’ll end up with peeling corners, uneven color, or worse, a floor that fails after the first winter. That’s a headache no one needs.
In this guide, I’ll show you exactly how to separate true professionals from part-timers. You’ll get clear questions to ask, red flags to watch for, and insights that could save you thousands. Let’s make sure your next project is something you’re proud to show off—not something you have to fix.
What is Epoxy Flooring?
Let’s start with the basics—because when you’re investing in your garage, you deserve to know exactly what you’re getting.
Epoxy flooring is a two-part system made of resin and hardener. When these components combine, they create a chemical bond that adheres to your concrete like nothing else. It doesn’t just sit on top of the surface. It fuses with it, locking in strength and durability.
Think of it as giving your garage a complete makeover that’s engineered for heavy use. Unlike standard paint or sealers, industrial epoxy flooring forms a dense, protective layer. It resists oil stains, road salt, and the hot tires that can peel lesser coatings right off the floor.
One of the biggest advantages? Epoxy doesn’t just cover flaws—it seals them out. Moisture, dirt, and chemicals are blocked from seeping into the concrete. This makes cleaning easier and helps your garage look sharp year-round.
In most residential garages, a professionally installed epoxy floor lasts anywhere from 10 to 15 years. Some hold up even longer with regular maintenance and the right prep work. That’s decades of reliable performance before you’ll need to think about recoating.
It’s not just about durability, though. A glossy, seamless finish transforms a dull space into something you’ll actually want to show off. Whether you’re parking your truck or setting up a workshop, epoxy flooring delivers a polished, professional look that’s built to last.
Why Choose a Professional Installer?
Benefits of Hiring an Expert
Let’s be honest—epoxy flooring isn’t just another weekend project. It’s a specialized process that demands skill, the right tools, and a commitment to doing it right the first time. Professional installers bring industrial-grade equipment to the table—think heavy-duty diamond grinders, high-powered vacuums, and commercial mixing systems. These aren’t items you can rent for a Saturday afternoon and expect showroom results.
More importantly, pros use premium materials you simply can’t buy off the shelf. That means thicker, more durable coatings that resist hot tire pickup, stains, and the freeze-thaw cycles that wreck DIY jobs. Most reputable installers back their work with warranties that protect you for years—sometimes a decade or more.
Time savings matter, too. What could take you several weekends (and endless trips to the hardware store) is usually completed in just one or two days by a professional team. You get a clean, usable space faster—without the headaches.
Top 5 Reasons to Hire a Pro:
Industrial Equipment: Pros use commercial diamond grinders and vacuums that create a perfect surface bond—no peeling or flaking later.
Premium Materials: Professional-grade epoxies and polyaspartics last years longer than store-bought kits.
Expert Preparation: Every step, from moisture testing to crack repair, is done right the first time.
Warranty Protection: Most professional installations come with robust warranties (often 10 years) you won’t get with DIY.
Time & Convenience: Enjoy a fast, hassle-free transformation without sacrificing weekends or risking costly mistakes.
Risks of DIY Epoxy Coatings
It’s tempting to think a DIY kit is a budget-friendly fix. But the reality is, cutting corners upfront usually costs more down the road. One of the biggest issues is peeling and hot tire pickup—when your tires lift the coating right off the concrete. This happens because store-bought kits don’t penetrate deeply or cure as hard as professional systems.
You also risk uneven finishes, bubbles, and spots that never fully dry. Worse, when DIY coatings fail, removing them is time-consuming and expensive. Many homeowners end up paying more to have a pro strip and redo the floor than if they’d hired an expert in the first place. And remember—most DIY products come with little to no warranty protection.
People Also Ask:
Q: Can I epoxy my garage floor myself?
You can, but it’s important to weigh the pros and cons:
Pros:
Lower upfront costs
Flexible timing if you want to tackle it over a few weekends
Basic improvement over bare concrete
Cons:
Limited durability—most kits only last 1–2 years
Higher chance of peeling, bubbling, and staining
No warranty coverage
Time-consuming preparation and application
Costly repairs if it fails
If you want a floor that performs—and looks great—long term, hiring a professional installer is almost always worth the investment.
Epoxy vs Polyurea: Which is Right for You?
If you’ve spent any time researching garage floor coatings, you’ve probably noticed one debate that keeps coming up: epoxy versus polyurea. Both options promise a smooth, resilient surface. But they perform differently—sometimes in ways that can make or break your floor’s success. Let’s break it down so you can decide what’s truly best for your space.
At a glance, epoxy is the long-trusted standard. It bonds deeply to prepared concrete, creating a thick, protective shell that resists abrasion, stains, and chemicals. Polyurea, on the other hand, has a faster cure time and higher flexibility, making it especially popular for climates with dramatic temperature swings.
When you look at the details side by side, it’s clear both epoxy and polyurea have strengths worth considering. Epoxy offers excellent durability for daily use and is easier on the budget, especially if you have a large garage or workshop to cover. It cures slower, which means installers have more time to create a flawless, decorative finish. But if you need your space back quickly, polyurea’s fast cure time is a big advantage—some floors are ready for light foot traffic within just a couple of hours. Polyurea also resists yellowing from sunlight and handles impact and scratches like a pro, making it a smart choice for high-traffic areas or garages exposed to UV rays. Just keep in mind that the speed of polyurea installation requires an experienced crew to get it right the first time.
Durability matters to everyone. But in the Midwest, you also have to think about salt, snow, and daily wear. Epoxy provides a thick, tough surface that holds up beautifully in garages and shops. Polyurea goes a step further with even greater flexibility and resistance to sudden temperature shifts. If your floor sees heavy vehicle use or direct sunlight, polyurea might be worth the added cost.
People Also Ask:
Q: Is epoxy or polyurea better for garage floors?
The honest answer—it depends on your priorities.
Epoxy Pros:
Time-tested performance in residential garages
More affordable for larger spaces
Longer working time during installation, which allows for detailed application and decorative finishes
Epoxy Cons:
Longer cure time before you can use the space
Can discolor over time if exposed to UV light
Polyurea Pros:
Cures incredibly fast—some projects are ready in a single day
Stays color-stable in sunlight
Exceptional flexibility to handle freeze-thaw cycles without cracking
Polyurea Cons:
Typically higher upfront cost
Fast set time requires a skilled installer—no room for mistakes
If you value speed and ultimate durability (especially in commercial settings or sun-exposed garages), polyurea is often the stronger choice. But if you prefer a more budget-friendly option with proven reliability, epoxy still delivers outstanding results when installed by a professional.
When in doubt, ask your installer to show you real samples and walk you through which system fits your climate, budget, and daily use. You deserve a floor that looks sharp and lasts for years—without surprises.
How Long Does Epoxy Flooring Last?
Here’s the question every homeowner wants answered before making the leap: how long will your new epoxy floor really last? In the Midwest, where temperatures swing from humid summers to subzero winters, longevity isn’t just a nice-to-have—it’s a necessity.
When installed professionally with proper preparation, epoxy floors can last 10 to 15 years in a garage that sees regular vehicle traffic. That means a decade or more of protection against salt, oil, hot tires, and the everyday wear that chews up bare concrete. If you’re using your space mostly for storage or as a workshop, you could see even longer performance—sometimes closer to 20 years with the right care.
But here’s what most people don’t realize: the lifespan of an epoxy coating is only partly about the product itself. The real secret is in the prep. Surfaces need to be diamond-ground to open the pores of the concrete and remove contaminants. Skipping this step or relying on acid etching almost always shortens the life of the coating.
Material quality matters, too. Industrial-grade epoxies have higher solids content, which means a thicker, more resilient layer that won’t peel or flake under pressure. Cheaper DIY kits often look fine for a year or two—but by the third winter, you’re likely to see chipping, bubbling, and those dreaded tire marks.
People Also Ask:
Q: How long does epoxy flooring last in a garage?
Most professionally installed epoxy garage floors last 10 years or more, especially when applied over well-prepped concrete and protected with a polyaspartic or urethane topcoat. In contrast, DIY kits may only hold up for 1–3 years before showing signs of failure.
If you’re investing in a floor that should look sharp and perform year after year, ask your installer about warranty coverage. A reputable contractor won’t just promise durability—they’ll back it up with a written guarantee that covers peeling, cracking, and yellowing.
What to Look for in an Epoxy Installer
Choosing the right installer isn’t just about finding the lowest bid. It’s about protecting your investment and making sure you don’t end up redoing your floor in a year. A polished website and a friendly voice on the phone are great starts—but you need more than promises. You deserve proof.
Start by confirming licenses and insurance. A reputable installer should hold all required state and local licenses. They should also carry liability and workers’ compensation insurance. This protects you if something goes sideways on the job. Don’t hesitate to ask for documentation. A trustworthy contractor will be happy to share it.
Next, look at local references and reviews. Real feedback from homeowners in your community is gold. Check Google, Yelp, and Facebook for detailed comments, not just star ratings. Look for mentions of communication, punctuality, and whether the floor held up over time—especially through Midwest freeze/thaw cycles.
Warranty coverage is another biggie. Some companies throw out the word “warranty” without explaining what it includes. Is it covering just material defects or installation errors too? How long does it last? You want a warranty that clearly spells out what’s protected, ideally in writing. In the Midwest, look for at least a 5–10 year guarantee against peeling, chipping, and discoloration.
Finally, ask for examples of past projects. Photos are good. Even better? An address you can drive by to see the results yourself. Professional installers are proud to showcase their work and should have a gallery of recent jobs. This is your chance to see their attention to detail up close—and to feel confident you’re trusting your floor to the right team.
Cost Breakdown and Pricing Transparency
Let’s talk dollars and sense. You’ve probably seen epoxy flooring advertised for everything from a few bucks a square foot to well over ten. The truth? Pricing varies—sometimes a lot—depending on what you need and who’s doing the work.
Ballpark price ranges for a professionally installed epoxy garage floor usually land between $5–$12 per square foot. That means a standard two-car garage might cost anywhere from $2,500 to $6,000, depending on materials and finish.
So, what drives the numbers up or down? Square footage is a major factor—bigger spaces often get a better per-foot rate. But don’t overlook prep work. If your concrete needs extensive crack repairs, moisture mitigation, or heavy grinding, expect a higher price tag. Those steps are critical. They ensure the coating actually bonds to the slab rather than peeling up after one winter.
And here’s the part no one likes to hear: cheapest isn’t always best. In fact, bargain-basement bids often skip proper prep or use low-grade materials that won’t last. A floor that fails in two years costs you more in the long run than investing in quality the first time. Always ask exactly what’s included in your quote—every layer, every step, every warranty term.
People Also Ask:
Q: How much does epoxy flooring cost per square foot?
On average, professional installation costs $5–$12 per square foot, depending on concrete condition, coating system, and decorative options. DIY kits can be cheaper upfront—around $1–$3 per square foot—but they rarely offer the same durability or finish quality.
Conclusion
Choosing the right epoxy installer isn’t just another checkbox on your renovation list—it’s the difference between a floor that peels in two years and one that stands strong for a decade or more. When you work with a qualified professional, you get more than a beautiful finish. You get meticulous surface preparation, premium-grade materials, and the peace of mind that comes with a real warranty.
Every detail matters. From how the concrete is cleaned and repaired to how the final topcoat is applied, the quality of your installer shapes the performance and lifespan of your investment. Don’t settle for shortcuts or vague promises.
Ready to transform your garage into a clean, polished space that holds up to everything the Midwest throws at it? Contact us today for a free, no-obligation estimate or explore our epoxy systems built to last. Your floors deserve the best.