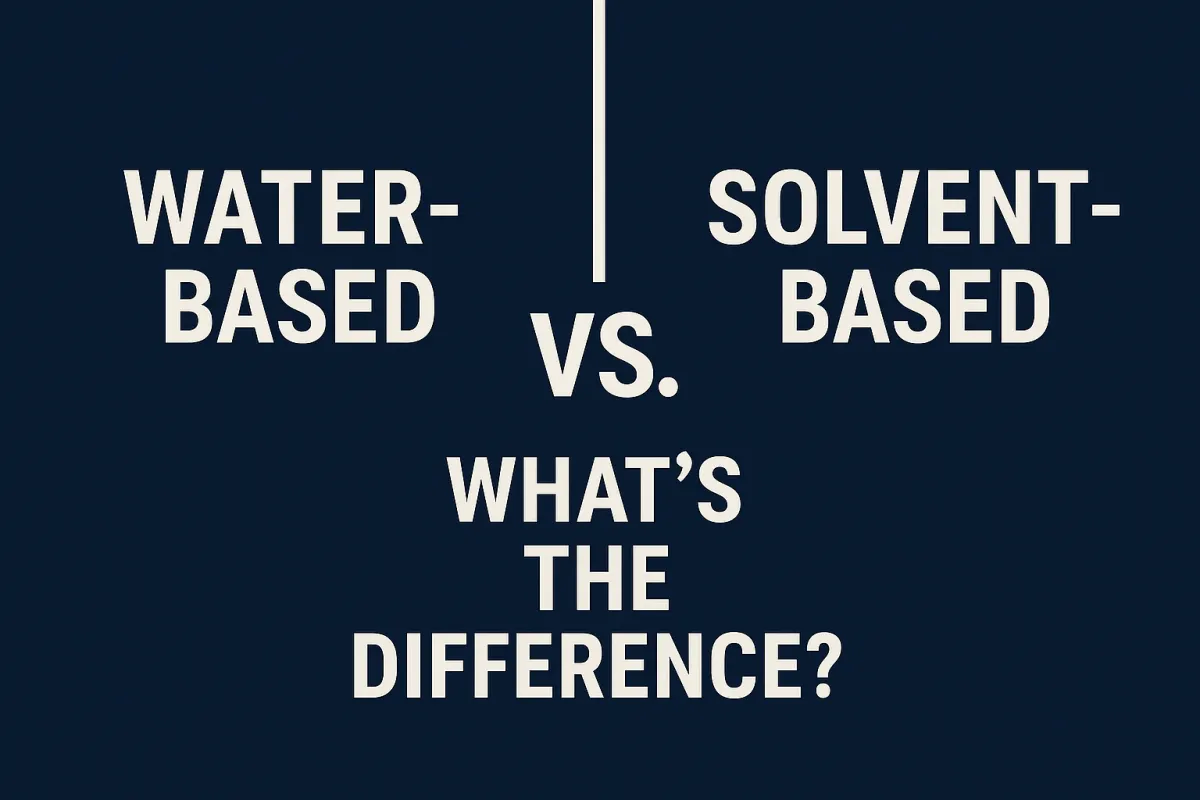
Water-Based vs. Solvent-Based Epoxy: What’s the Difference?
When it comes to protecting your concrete floors, not all epoxy coatings are created equal. Whether you're looking to upgrade a garage, basement, or commercial workspace, understanding the difference between water-based epoxy and solvent-based epoxy is key to getting a floor that lasts.
These two types may seem similar, but they perform very differently in terms of durability, appearance, and application. Choosing the wrong one can lead to premature wear, wasted money, and frustration—especially in climate-intense regions like the Midwest.
In this complete guide, we’ll break down:
What water-based epoxy really is
What makes solvent-based epoxy stronger (but more challenging)
When to use one over the other
Common pitfalls and myths
How to make the right decision for your space
Let’s dive in.
Water-Based vs. Solvent-Based Epoxy: What’s the Difference?
Key Differences: Water vs. Solvent-Based
Which One Is Best for Your Space?
Midwest Climate Considerations
Our Pro Process Often Includes:
Is water-based epoxy bad for garages?
Does solvent-based epoxy smell bad?
How long do these coatings last?
What Is Water-Based Epoxy?
Water-based epoxy is a two-part coating system where water acts as the carrier for the epoxy resins instead of solvents. This creates a more user-friendly product that releases fewer harmful emissions during application and curing. The system consists of an epoxy resin (Part A) and a water-based curing agent (Part B) that, when mixed, create a chemical reaction resulting in a durable—though relatively thinner—protective floor coating.
Technical Specifications
Solids content: Typically 30-60% (meaning up to 70% evaporates during curing)
Dry film thickness: 2-3 mils per coat (approximately 0.002-0.003 inches)
Pot life: Usually 1-2 hours after mixing (longer than solvent-based options)
Recommended coats: Minimum 2-3 for adequate protection
Full cure time: Touch dry in 4-8 hours, light foot traffic in 24 hours, full cure in 5-7 days
Expected lifespan: 2-4 years in moderate traffic areas, less in high-traffic zones
Temperature requirements: Application between 50-90°F with humidity below 80%
Application Process
Water-based epoxy is more forgiving during application than other types, making it suitable for DIY projects:
Preparation: Clean and etch the concrete surface (acid etching kits are available at home improvement stores)
Priming: Some systems require a primer coat for better adhesion
Mixing: Combine Part A and Part B according to manufacturer instructions (typically a 3:1 or 4:1 ratio)
Application: Roll on using a 3/8" nap roller in manageable 10x10 foot sections
Second coat: Apply after first coat is dry to touch (usually 4-8 hours) but within 24 hours for proper adhesion
Optional clear coat: A urethane top coat can significantly extend durability and UV resistance
Cost Breakdown
Materials: $30-60 per gallon, covering approximately 250-300 square feet per gallon
Complete DIY project: $0.40-$1.50 per square foot (depending on number of coats)
Professional installation: $3-5 per square foot (including preparation and application)
Annual cost when amortized: Approximately $1-2.50 per square foot per year (considering reapplication needs)
Pros:
Low odor and VOCs: Safe for use in homes with minimal ventilation, making it ideal for indoor projects where fumes would be problematic.
Easy cleanup: Tools can be washed with soap and water while the product is still wet, eliminating the need for harsh solvents.
Good adhesion: Works well on slightly porous or moisture-prone surfaces where other epoxies might fail. Can tolerate slightly higher moisture content in concrete (up to 8% compared to 3-5% for other epoxies).
Affordable: A solid option for budget-conscious projects, with material costs 20-40% lower than solvent-based alternatives.
Environmentally friendlier: Significantly lower VOC content (typically <100 g/L compared to 400-600 g/L in solvent-based options) helps meet environmental regulations and reduces ecological impact.
Shorter downtime: Faster application and cure times mean spaces can return to service more quickly.
More forgiving application: Better tolerance for application errors and varying temperature conditions makes it more suitable for DIY projects.
Cons:
Thinner film build: Less resistance to scratches, chemicals, and abrasion due to lower solids content and reduced thickness per coat.
Limited durability: Especially under vehicle traffic or hot tire pickup, which can cause the coating to soften and peel.
Shorter life span: Typically needs re-coating within a few years in high-traffic zones, creating higher long-term maintenance costs.
Reduced chemical resistance: Less effective against harsh chemicals, petroleum products, and extended exposure to automotive fluids.
Temperature sensitivity during cure: Can bubble or fail to cure properly in high humidity or temperatures below 50°F.
Less glossy finish: Typically produces a more satin or semi-gloss appearance rather than the high-gloss look of solvent-based or 100% solid systems.
Prone to water spotting: Early exposure to water during curing can cause permanent spotting or cloudiness in the finish.
Ideal Applications:
Finished basements: Provides dust control and moderate moisture resistance with minimal odor during application.
Light-use garages: Suitable for storage areas or garages where vehicles are parked only occasionally.
Utility rooms: Offers improved cleanability and moderate chemical resistance for laundry spills.
Rental properties: Provides a cost-effective floor upgrade that can be easily refreshed between tenants.
Home workshops: Creates a cleaner environment for woodworking or hobby activities with moderate tool traffic.
Enclosed patios: Offers UV resistance superior to bare concrete while remaining breathable.
Retail spaces: Provides an economical floor solution for shops with primarily foot traffic.
Office environments: Creates a professional appearance with good daily-wear resistance in low-impact settings.
Seasonal spaces: Perfect for three-season rooms or spaces not subjected to extreme temperature fluctuations.
Extending Water-Based Epoxy Performance
Several strategies can help maximize the lifespan of water-based epoxy floors:
Apply additional coats: Each additional coat increases durability, with three coats offering nearly twice the wear resistance of two.
Add a clear topcoat: A urethane or polyaspartic clear coat can dramatically improve scratch resistance and UV stability.
Use proper cleaning protocols: Avoid harsh cleaners; instead, use pH-neutral floor cleaners and microfiber mops.
Install entry mats: Capturing abrasive dirt and debris at entrances significantly reduces wear patterns.
Apply annual maintenance coats: A light "refresh coat" every 1-2 years can extend the system's life substantially without requiring complete removal and reapplication.
Common Application Mistakes to Avoid
Inadequate surface preparation: Skipping proper cleaning, etching, or grinding is the leading cause of water-based epoxy failures.
Applying over sealed concrete: Water-based epoxy needs porosity for proper adhesion; it will fail quickly over sealed surfaces.
Mixing too much at once: Only mix what can be applied within 60-90 minutes to prevent waste and application issues.
Applying too thinly: Stretching the product too far reduces film thickness and compromises durability.
Ignoring temperature guidelines: Application below 50°F or above 90°F significantly affects cure time and adhesion.
When to Choose Water-Based Epoxy
Water-based epoxy is the right choice when:
You need a DIY-friendly option requiring minimal specialized skills
Indoor air quality concerns make solvent-based products problematic
The project is short-term or has budget constraints
The floor will see primarily foot traffic rather than heavy equipment or vehicles
You need a quicker return to service than other epoxy systems allow
Environmental regulations limit VOC emissions in your area
Slight concrete moisture issues exist that would compromise solvent-based products
Water-based epoxy represents an excellent entry point into concrete floor coatings, offering a balance of performance and accessibility that makes it particularly suitable for homeowners and light commercial applications where extreme durability isn't the primary concern.
What Is Solvent-Based Epoxy?
Solvent-based epoxy is also a two-part system, but instead of water, it uses chemical solvents to carry the epoxy resin. These coatings cure to form a much thicker, harder, and glossier surface that’s highly resistant to damage.
Pros:
Superior strength: Tougher against chemicals, abrasion, and hot tires.
Glossy, showroom finish: Great for visual appeal in garages or commercial settings.
Pro-grade performance: Trusted by contractors for heavy-duty applications.
Cons:
High VOCs and strong odor: Requires proper ventilation and protective equipment during application.
Application challenges: Not ideal for DIYers without experience.
UV sensitivity: Can yellow over time in sunlight without a UV-stable topcoat.
Ideal Applications:
Automotive garages
Warehouses and workshops
Commercial spaces
Residential garages with heavy traffic
Key Differences: Water vs. Solvent-Based Epoxy
When choosing between water-based and solvent-based epoxy systems, understanding their fundamental differences helps you select the right coating for your specific needs. While they may look similar when first applied, these two formulations differ significantly in composition, performance, and practical considerations.
Chemical Composition & Formulation
Water-Based Epoxy: These systems use water as the primary carrier medium for the epoxy resins. Water-based formulations typically contain 30-60% solids, with water making up a significant portion of the volume. This water evaporates during the curing process, leaving behind a thinner epoxy film.
Solvent-Based Epoxy: These use chemical solvents (like xylene, toluene, or MEK) as carriers for the epoxy resins. Solvent-based formulations typically contain 40-70% solids, with solvents evaporating during curing to leave a thicker, more chemical-resistant coating. The solvents allow for deeper penetration into the concrete surface.
Environmental & Safety Factors
VOC Emissions:
Water-Based: Typically 50-250 g/L of VOCs (Volatile Organic Compounds), making them compliant with most regional regulations and suitable for occupied buildings.
Solvent-Based: Can contain 400-700 g/L of VOCs, requiring significant ventilation during application and often making them non-compliant with stringent environmental regulations in some areas.
Odor During Installation:
Water-Based: Mild, slightly sweet odor that dissipates quickly, often allowing nearby areas to remain occupied during installation.
Solvent-Based: Strong, chemical odor that can persist for days and may require temporary relocation of building occupants. Proper respiratory protection is essential during application.
Flash Point & Fire Safety:
Water-Based: Non-flammable with no flash point, making them safer to store and apply without special fire precautions.
Solvent-Based: Flammable during application with low flash points, requiring careful handling, prohibition of open flames or sparks, and special storage considerations.
Applicator Health Risks:
Water-Based: Minimal exposure concerns beyond standard protective equipment (gloves, eye protection).
Solvent-Based: Requires extensive PPE including organic vapor respirators, and may cause headaches, dizziness, or long-term health effects with repeated exposure.
Performance Characteristics
Film Thickness & Build:
Water-Based: Typically yields 2-3 mils per coat with limited build properties.
Solvent-Based: Achieves 3-5 mils per coat with better self-leveling and build characteristics.
Durability Factors:
Water-Based: Moderate abrasion resistance suitable for residential and light commercial use; typically lasts 2-4 years before showing significant wear.
Solvent-Based: High abrasion resistance appropriate for commercial and industrial applications; can last 4-7 years with proper maintenance.
Chemical Resistance:
Water-Based: Provides basic resistance to household cleaners and occasional spills but breaks down with prolonged exposure to harsh chemicals or petroleum products.
Solvent-Based: Offers superior resistance to oils, fuels, acids, and industrial chemicals, making it suitable for automotive and manufacturing environments.
UV Stability:
Water-Based: Generally more UV stable with less yellowing over time, making them better for areas with significant natural light.
Solvent-Based: More prone to ambering (yellowing) with UV exposure unless specifically formulated with UV inhibitors.
Hot Tire Resistance:
Water-Based: Limited resistance to hot tire pickup; may soften and peel under hot tires from vehicles recently driven.
Solvent-Based: Significantly better resistance to hot tire pickup, maintaining adhesion even with hot rubber contact.
Application Considerations
Surface Preparation Requirements:
Water-Based: Can tolerate slightly higher moisture content in concrete (up to 8%) and work with less aggressive surface preparation in some cases.
Solvent-Based: Typically requires concrete moisture content below 5% and thorough mechanical preparation (grinding or shot blasting).
Ease of Use:
Water-Based: Easier for DIY application with longer working time (pot life typically 1-2 hours) and forgiving application properties.
Solvent-Based: More technically challenging with shorter working time (pot life often 30-60 minutes) and less forgiving of application errors.
Temperature Range for Application:
Water-Based: Narrower application window, typically 50-90°F, with potential issues below 50°F.
Solvent-Based: Wider application temperature range, often 40-100°F, making them more versatile in varied climate conditions.
Dry/Cure Times:
Water-Based: Touch dry in 4-8 hours, recoat window of 12-24 hours, walkable in 24 hours, full cure in 5-7 days.
Solvent-Based: Touch dry in 6-12 hours, recoat window of 12-24 hours, walkable in 24-36 hours, full cure in 7-10 days.
Concrete Adhesion:
Water-Based: Good adhesion to properly prepared surfaces, but less penetrating power into dense concrete.
Solvent-Based: Excellent adhesion with deep penetration into the concrete substrate, creating a stronger mechanical bond.
Aesthetic Differences
Finish Options:
Water-Based: Typically available in matte, satin, and semi-gloss finishes; full high-gloss is harder to achieve.
Solvent-Based: Readily available in high-gloss finishes with deeper, richer appearance and better light reflection.
Color Retention:
Water-Based: Better long-term color stability, especially in lighter shades.
Solvent-Based: Initial colors appear richer but may amber slightly over time.
Depth and Clarity:
Water-Based: Tends to look more "plastic-like" with less visual depth.
Solvent-Based: Creates a "wetter" look with more apparent depth and richness.
Light Reflectivity:
Water-Based: Moderate light reflection that diminishes somewhat as the coating ages.
Solvent-Based: Higher initial light reflection that can enhance space brightness significantly.
Economic Considerations
Initial Material Cost:
Water-Based: $30-60 per gallon, covering 250-300 sq ft per gallon.
Solvent-Based: $45-90 per gallon, covering 250-300 sq ft per gallon.
Installation Labor:
Water-Based: Lower labor costs due to simpler application and cleanup procedures.
Solvent-Based: Higher labor costs reflecting more intensive preparation, application complexities, and cleanup requirements.
Long-Term Value:
Water-Based: Higher lifetime cost when factoring in more frequent reapplication needs.
Solvent-Based: Often better long-term value despite higher initial investment due to extended service life.
Maintenance Requirements:
Water-Based: More frequent maintenance with potential refresher coats needed every 1-2 years.
Solvent-Based: Less frequent maintenance with touch-ups typically needed only every 3-5 years.
Best-Fit Applications
Water-Based Epoxy Excels In:
Residential basements and living spaces
Office environments
Retail spaces with primarily foot traffic
Areas requiring quick turnaround time
Projects with strict VOC regulations
DIY applications by homeowners
Spaces with limited ventilation during installation
Areas needing frequent color changes or updates
Solvent-Based Epoxy Excels In:
Commercial garages and workshops
Industrial facilities
Areas with frequent chemical exposure
Spaces with hot tire traffic
High-demand environments requiring maximum durability
Applications requiring maximum concrete penetration and adhesion
Projects where long-term performance outweighs initial cost considerations
Environments with extreme temperature variations
Making Your Selection
When deciding between water-based and solvent-based epoxy, consider:
Usage Requirements: Assess the actual wear and exposure your floor will experience.
Environmental Factors: Consider ventilation, occupied spaces, and local VOC regulations.
Budget Balance: Weigh initial costs against long-term performance and maintenance needs.
Aesthetic Goals: Determine if the appearance differences align with your design vision.
Installation Timeline: Factor in cure times and how quickly the space needs to return to service.
Application Expertise: Honestly evaluate whether the project matches your skill level if considering DIY.
For most residential applications with moderate traffic, water-based epoxy provides an acceptable balance of performance and value. However, for areas with vehicles, heavy equipment, or frequent spills, the additional investment in solvent-based epoxy typically pays dividends through significantly extended service life and reduced maintenance requirements.
Understanding these key differences helps ensure you select the right epoxy system for your specific needs, balancing immediate concerns like cost and installation complexity against long-term factors like durability and maintenance requirements.
Which One Is Best for Your Space?
Choosing the right epoxy comes down to three main factors: ventilation, durability needs, and ease of installation.
Ask Yourself:
Is the area well-ventilated?
→ Choose solvent-based if yes.
→ Stick with water-based if not.Will the floor handle hot tires, tool drops, or chemical spills?
→ Solvent-based is better for long-term durability.Are you looking for a fast, low-odor project?
→ Water-based wins for quick, easy application.
Midwest Climate Considerations
In colder states like Minnesota, Iowa, or Wisconsin, your floors face freeze-thaw cycles, salt exposure, and humidity. Solvent-based systems tend to perform better long-term under these conditions. They provide:
Greater resistance to flaking and bubbling
Higher adhesion even with moisture in the slab
Longer-lasting shine and finish retention
Water-based systems are still an option—but only in interior, temperature-stable rooms or for cosmetic applications.
Expert Advice from DreamWorx
Still not sure which direction to go?
At DreamWorx Concrete Coatings, we evaluate:
The age and condition of your concrete
Moisture levels in your slab
Your traffic patterns and use cases
Whether appearance, durability, or speed matters most
Our Pro Process Often Includes:
MVB Primer (Moisture Vapor Barrier) – especially for basements or damp garages
Solvent-Based Epoxy Base – for strength and adhesion
Polyaspartic Topcoat – for UV stability and fast cure
This multi-layer approach ensures your floor isn’t just coated—it’s protected for the long haul.
FAQs About Epoxy Coatings
Is water-based epoxy bad for garages?
Not bad, just limited. It works in low-traffic or storage-only garages, but won’t hold up to cars and equipment as well as solvent-based systems.
Does solvent-based epoxy smell bad?
Yes—but it’s temporary. With proper airflow, the smell clears up quickly after application and curing.
How long do these coatings last?
Water-Based: 3–5 years in light-use areas
Solvent-Based: 7–15 years or longer, depending on prep and maintenance
Can I recoat or upgrade later?
Yes. You can always upgrade from water-based to solvent-based later, though it may require extra surface prep.
Are both safe after curing?
Absolutely. Once fully cured, both types are safe, non-toxic, and easy to clean.
Get a Professional Opinion
Choosing between water-based and solvent-based epoxy isn’t just about chemistry—it’s about what works for your lifestyle, property, and long-term goals.
That’s where DreamWorx comes in.
Why Choose Us?
✅ Transparent pricing
✅ Installed in 1–2 days
✅ Premium-grade materials
✅ Midwest-tested solutions
✅ 10-year warranty
We make concrete beautiful, durable, and worry-free—without cutting corners.
Book your free on-site estimate today to get expert advice, transparent pricing, and a personalized flooring recommendation. Whether you’re upgrading your garage, basement, or commercial space, we’ll help you choose the right coating system for lasting performance and peace of mind.