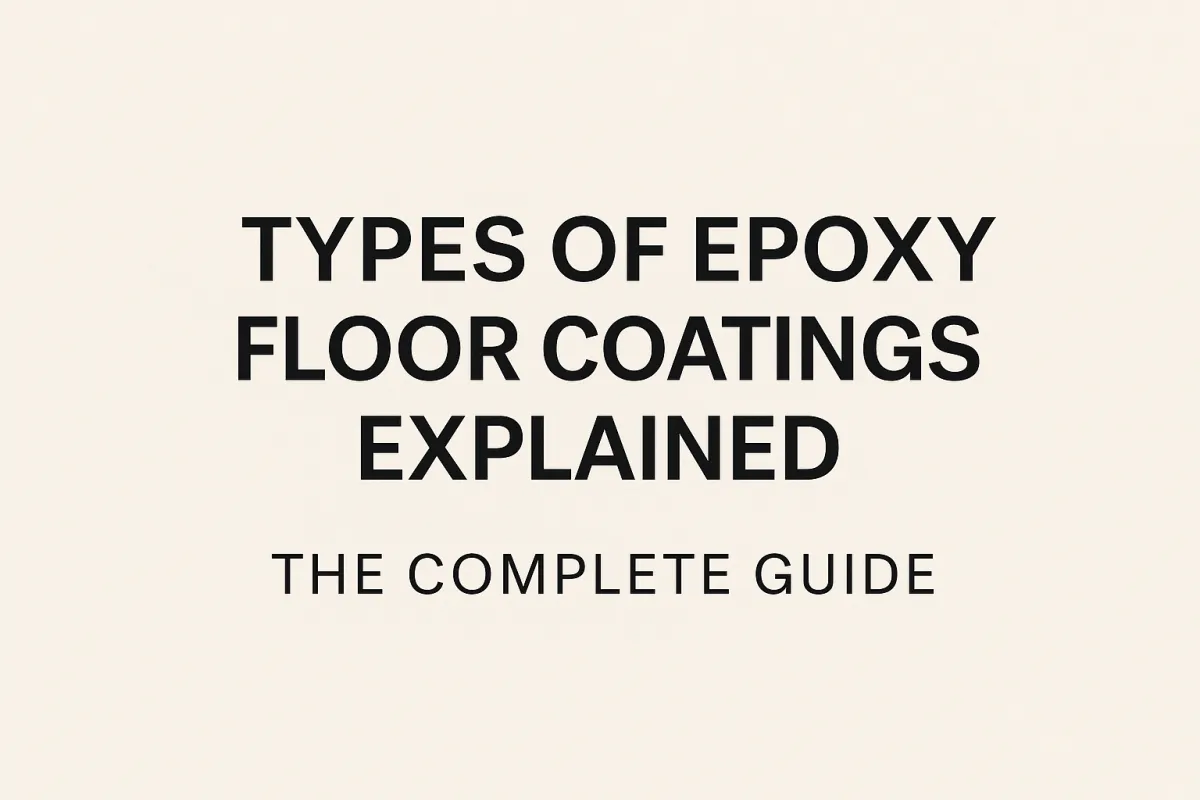
Types of Epoxy Floor Coatings Explained: The Complete Guide
If you're exploring ways to upgrade your garage, basement, or commercial floor, epoxy coatings aren't just an option—they're a game changer. That sad, cracked concrete floor with mysterious stains can be transformed into a showroom-quality surface that's both functional and beautiful.
Not all epoxy floors are created equal. From quick DIY kits to professional-grade multi-layer systems, the type of epoxy you choose dramatically impacts durability, aesthetics, and performance—especially in the Midwest, where our seasons put everything to the test.
Think of epoxy coatings as armor for your concrete. The right epoxy transforms a porous, dusty slab into a sealed, chemical-resistant surface that can handle everything from hot tire marks to spilled chemicals without damage. Whether for your home garage or commercial facility, this guide breaks down the most common types of epoxy floor coatings to help you make an informed decision.
Types of Epoxy Floor Coatings Explained: The Complete Guide
2. Solvent-Based Epoxy Coatings
6. MVB (Moisture Vapor Barrier) Epoxy
The Cost of Skipping This Step
7. Which Epoxy is Right for You?
For Budget-Conscious Protection
For Commercial Kitchens & Wet Areas
8. The Value of Professional Installation
Why Professional Installation Matters
1. Water-Based Epoxy Coatings
Best For: DIYers, light-use areas, or concrete that needs to "breathe"
Water-based epoxy is the most beginner-friendly option. It combines epoxy resins with water as a carrier, resulting in a thinner consistency that's easier to apply but doesn't build up as thick as other options.
How It Works
The water evaporates during curing, leaving behind a protective layer that provides basic protection and aesthetic improvement. It's less potent than other formulations, making it suitable for indoor applications where ventilation might be limited.
Technical Details
Thickness: Typically thin (about the thickness of a trash bag per coat)
Cure time: Initial cure in 4-8 hours, but takes 5-7 days for full hardness
Typical uses: Laundry rooms, home offices, low-traffic areas
Pros:
Low odor and fewer harmful fumes
Easy cleanup with just soap and water
Less expensive than other options
DIY-friendly application
Environmentally friendlier option
Cons:
Wears more quickly under regular use
Less chemical resistance
Not ideal for garages with parked vehicles
Requires more coats for adequate protection
May not hold up well in humid conditions
Real Talk
While the initial cost is lower, you'll likely need to recoat every 2-3 years in average conditions, more frequently in high-traffic areas. If budget is your main concern, water-based epoxy gives you a decent starting point, but don't expect long-term performance in demanding environments.
2. Solvent-Based Epoxy Coatings
Best For: Moderate-use garages, workshops, and spaces needing better chemical resistance
Solvent-based epoxies provide a significant step up in durability. These formulations use chemical solvents to carry the epoxy resins, creating a stronger bond with the concrete and a harder finish.
How It Works
The solvent helps the coating penetrate deeper into concrete pores before evaporating during curing. This leaves behind a thicker, more durable coating that stands up better to automotive fluids, moderate impacts, and regular cleaning.
Technical Details
Thickness: Moderate thickness per coat
Cure time: Typically 8-24 hours between coats, 5-7 days for full cure
Typical uses: Family garages, workshops, utility rooms
Pros:
More durable than water-based options
Creates an attractive glossy finish
Better resistance to automotive fluids and chemicals
Resists hot tire pickup better
Good middle ground between DIY and professional systems
Cons:
Stronger odor during installation requires proper ventilation
Can yellow over time with UV exposure
Requires more careful application
Contains more VOCs (volatile organic compounds)
Requires solvents for cleanup
Practical Considerations
If your garage doubles as a weekend project space or parking area, solvent-based epoxy offers meaningful protection from occasional oil drips and the movement of tools and equipment—situations where water-based would quickly show damage.
3. 100% Solid Epoxy Coatings
Best For: High-performance spaces, commercial applications, and "do it once, do it right" projects
100% solid epoxy is the heavyweight champion of floor coatings. As the name suggests, there are no carriers that evaporate—what you apply is what stays on the floor, creating a thick, industrial-grade surface.
How It Works
Without water or solvents to evaporate, these systems cure through a chemical reaction between the resin and hardener. The result is a much thicker coating that can be built up to impressive depths, offering maximum protection and longevity.
Technical Details
Thickness: Very thick (3-10 times thicker than water-based per coat)
Impact resistance: Excellent, can withstand dropped tools and heavy equipment
Typical uses: Commercial spaces, high-end garages, industrial facilities
Pros:
Maximum durability for demanding environments
Excellent resistance to impacts, chemicals, and moisture
Customizable thickness based on needs
Often includes warranty protection
Permanently reduces concrete dust and maintenance
Available in many color options
Cons:
Requires professional installation
Higher upfront investment
Unforgiving of improper concrete preparation
Very slippery when wet unless additives are incorporated
Value Consideration
While the upfront cost is higher, the long-term value is excellent, with many installations lasting 10-20 years with proper maintenance. When calculated over its lifespan, a 100% solid system often costs less than repeatedly applying lesser products.
4. Metallic Epoxy Floors
Best For: Luxury spaces, showrooms, and anyone who wants truly distinctive flooring
If you want floors that make visitors say "wow," metallic epoxy delivers. These aren't just floors; they're conversation pieces that transform ordinary concrete into fluid, three-dimensional masterpieces.
How It Works
Metallic epoxy systems typically use a 100% solids epoxy base with added metallic pigment particles. These particles create incredible depth and movement patterns that resemble flowing lava, marble, or even planetary surfaces.
Unique Installation Process
No two metallic floors are exactly alike because the installation process combines technical expertise and artistic technique. Installers use various methods to create different effects, resulting in truly one-of-a-kind floors.
Ideal Applications
High-end residential living spaces
Office lobbies and reception areas
Upscale retail environments
Restaurant dining rooms
Entertainment spaces and basement renovations
Pros:
Creates a truly unique, high-gloss appearance
Offers unlimited custom color combinations
Becomes a signature design element of the space
Builds on the durability of 100% solid systems
Hides minor concrete imperfections
Creates a memorable impression
Cons:
Higher cost than standard epoxy systems
Can be slippery if not properly top-coated
Requires highly skilled installers
More difficult to repair if damaged
Longer installation process
Practical Benefits
Beyond pure aesthetics, metallic floors offer practical advantages:
The depth and movement mask dirt and dust between cleanings
The patterns disguise minor wear that would be obvious on solid-color floors
They increase perceived value in real estate settings
5. Quartz-Filled Epoxy
Best For: Commercial kitchens, gyms, locker rooms, and areas needing slip resistance
Quartz epoxy systems combine safety with durability. These industrial-strength flooring solutions incorporate colored quartz granules into the epoxy matrix, creating a textured, extremely durable surface.
How It Works
A base coat of epoxy is applied, then broadcast (scattered) with quartz aggregate until completely covered. After curing, excess quartz is removed, and clear topcoats seal everything in place.
Technical Details
Thickness: Thicker overall system (typically 1/8" to 1/4")
Slip resistance: Excellent, even when wet
Load capacity: Suitable for heavy equipment and high traffic
Ideal Applications
Commercial kitchens and food processing
Locker rooms and shower areas
Healthcare facilities and laboratories
Automotive service areas
Any environment where slip-resistance is critical
Pros:
Textured, non-slip finish even when wet
Extremely durable under constant foot traffic
Both functional and decorative
Hides dirt between cleanings
Withstands temperature changes better than smooth epoxy
Meets health department requirements in commercial settings
Cons:
More industrial appearance
Multi-step application process requiring expertise
More challenging to clean than smooth surfaces
Higher material cost than basic systems
Safety Consideration
Beyond durability, the primary advantage of quartz systems is safety. Slip-and-fall incidents are costly liabilities, making the investment in proper flooring a risk management decision as much as an aesthetic one.
6. MVB (Moisture Vapor Barrier) Epoxy
Best For: Basements, ground-level installations, or any concrete with moisture concerns
MVB epoxy isn't about looks—it's the critical foundation that prevents flooring failures. These specialized formulations prevent water vapor from rising through the concrete slab, which is essential in areas with moisture issues.
The Hidden Moisture Problem
Concrete is porous, and even fully cured concrete continues to transmit water vapor. When that vapor gets trapped under an impermeable coating like epoxy, it creates pressure that can cause bubbling, peeling, and complete system failure—often within months of installation.
How MVB Works
These specialized formulations create a barrier that blocks vapor transmission while still allowing proper adhesion for subsequent coating layers. Think of it as waterproofing that makes everything else possible.
When MVB Is Essential
Concrete less than 1 year old
Basements or slabs below grade
Areas with known moisture issues
Concrete without proper vapor barriers underneath
Spaces that have experienced previous coating failures
Most installations in humid climates
Pros:
Prevents bubbling, peeling, and delamination from moisture
Required for warranty validity with many systems
Adds significant longevity to all types of floor coatings
Solves problems in historically "difficult" concrete
Makes finished floors more resistant to moisture pressure
Cons:
Must be paired with another coating system for a finished look
Adds time to installation process
Increases initial project cost
The Cost of Skipping This Step
Adding MVB adds to the project cost, but skipping it when needed can result in complete system failure requiring removal and reinstallation—often at 2-3 times the original project cost. Professional installers will test your concrete's moisture levels to determine if MVB is necessary.
7. Which Epoxy is Right for You?
Now that we've covered the major epoxy types, here's how to choose based on your specific needs:
For Maximum Durability
If your priority is flooring that stands up to extreme use:
Best choice: 100% Solid Epoxy or Quartz-Filled Systems
Expected lifespan: 10-20 years with proper maintenance
Perfect for: High-traffic commercial, industrial, and serious residential applications
For Stunning Appearance
If you're focused on creating a visual impression:
Best choice: Metallic Epoxy
Expected lifespan: 7-15 years depending on traffic
Perfect for: Showrooms, luxury homes, and statement commercial spaces
For Budget-Conscious Protection
If you need basic protection without a major investment:
Best choice: Water-Based or Solvent-Based Epoxy
Expected lifespan: 2-5 years depending on traffic
Perfect for: Seasonal spaces, light-use areas, or temporary solutions
For Moisture-Prone Areas
If you're dealing with basement or ground-level installations:
Best first layer: MVB (Moisture Vapor Barrier)
Then top with: Any of the above systems based on other priorities
For Commercial Kitchens & Wet Areas
If slip resistance and sanitation are primary concerns:
Best choice: Quartz-Filled Epoxy
Expected lifespan: 8-15 years in demanding environments
Perfect for: Food service, locker rooms, healthcare, and areas with spill potential
8. The Value of Professional Installation
While DIY epoxy kits promise easy weekend projects, professional installation makes an enormous difference in longevity and appearance—especially for higher-grade systems.
Why Professional Installation Matters
Proper surface preparation – Up to 80% of epoxy failures stem from inadequate preparation
Moisture testing and mitigation – Professionals identify invisible issues before they become costly problems
Temperature and humidity control – Experts understand how environmental factors affect curing
System selection expertise – Recommendations based on your specific concrete condition and usage patterns
Warranty protection – Quality installations include warranty coverage
The Professional Installation Process
Most professional installations follow this schedule:
Day 1: Preparation (grinding, crack repair, moisture testing)
Day 2-3: Base coat and/or build coat application
Day 4: Topcoat application and detail work
Day 5-7: Cure time before returning to full service
Long-Term Value
While professional installation costs more initially, the extended lifespan, reduced maintenance, and elimination of costly failures make it the more economical choice over time. Professional installers provide free consultations to help you determine the right system for your specific needs.
Next Steps
Contact your local professional epoxy flooring contractor today for a free on-site assessment and custom quote. They can help you select the right system for your space and provide a detailed estimate for professional installation.
Transform your concrete from ordinary to extraordinary with the right epoxy system professionally installed by experienced craftsmen who stand behind their work.